Науглероживание металла в домашних условиях. Что такое цементация стали и как ее сделать в домашних условиях? Газовая цементация – оптимальный вариант для массовой обработки изделий
Химико-термическая обработка стали | Обработка металла – стали и цветных металлов
Такая обработка металла изменяет не только лишь его структуру, а и хим состав его поверхности. Благодаря этому деталь может иметь вяжущую сердцевину, которая выдерживает ударные нагрузки, и высшую твердость и стойкость против воздействия снаружи. Существует несколько методов химико-термической обработки, но в критериях маленький мастерской (тем паче в домашних критериях) можно выполнить только цементацию.
Цементация – насыщение углеродом поверхностного слоя стали без доступа воздуха, в среде (карбюризаторе), котороя имеет существенное содержимое углерода. Цементируют обычно детали из малоуглеродных сталей, которые после закала поверхностного слоя шлифуют. Карбюризаторы для цементации поверхностного слоя стали могут иметь различный состав, но простой таковой, %:
Углекислый натрий либо углекислыйбарий (для ответственных деталей) ………10Углекислый кальций……………………………..3Древесный уголь…………………………………..87
Карбюризатор можно приготовить из углекислого натрия (сода 6-10 %) и пиленного рога либо торфяного кокса ( 90-94 %). Маленькие либо одиночные детали цементируют в пасте, которая состоит из таких компонент, %:
Газовая сажа……………………………………….28Кальцинированная сода………………………3,5Желтоватая кровяная соль………………………..1,5Веретенное масло……………………………….67илиГолландская сажа………………………………30Кальцинированная сода……………………….10Веретенное масло………………………………40Декстрин (клей) ………………………………..20
Неплохую пасту для цементации можно приготовить из художественной краски «Газовая сажа» (продают в тюбиках), к которой домешивают часть за массой кальцинированной соды.Места на деталях, которые не нуждаются в цементации, защищают противо-цементационными обмазками. Простая обмазка – это огнеупорная глина с добавкой (10 %) асбестового боя. Замешивают смесь на воде. Комфортная в использовании и такая обмазка, %: тальк-50, каолин – 25, вода – 25.Разводят эту обмазку к подходящей плотности водянистым стеклом либо конторским силикатным клеем. Закладывают детали в цементационные ящики после высыхания обмазки. Цементируют так. В железный ящик с крышкой на дно насыпают карбюризатор слоем 30— 40 мм и на него кладут приготовленные (обмазанные) детали таким образом, чтоб расстояние меж ними, также меж ними и стенами ящика сотовляла около 10-15 мм. Сверху детали присыпают карбюризатором слоем 30—40 мм, закрывают крышкой, промазывают ее кромки огнеупорной глиной и сушат.Если для цементации используют пасту, то деталь намазывают ею слоем толще 3-4 мм, кладут в ящик, закрывают и также обмазывают кромки крышки огнеупорной глиной. После высыхания глины ящик помещают в печь и выдерживают (температуры 930—950 °С) в протяжении 1,5-3 года (с жестким карбюризатором 7-8 лет). При всем этом слой цементации добивается 1 мм. Время от времени в ящике для цементации делают отверстия и в них вставляют 1-2 отрезка мягенького железного провода поперечником 3-4 мм (пробник). Щели отлично обмазывают огнеупорной глиной. Спустя некое время пробник вынимают, отверстие замазывают глиной, а пробник переризают и определяют глубину цементации, т.е. необходимость предстоящего прогревания. После цементации детали охлаждают вкупе с ящиком, позже нагревают до температуры 760— 780 °С. и закаливают. Облегченная цементация. Маленькие детали из малоуглеродных сталей цементируют такими методами:желтоватой кровяной солью ( железо-цианистый калий). Для цементации деталь нагревают, обсыпают солью и опять нагревают до расплавления соли (850 °С), позже вынимают и закаливают. При всем этом слой цементации сравнимо маленькой – около 0,15 мм. Если нужно прирастить его, деталь обсыпают солью и нагревают при обозначенной температуре в протяжении 1 ч, позже сразу закаливают, металлическими опилками. Это старенькый кузнечный метод «укрепление в горне». Подогретую к белоснежному цвету деталь, не вынимая из горна, очищают проволочной щеткой и присыпают металлическими опилками, из которых углерод перебегает на поверхность детали. Очищение и присыпания повторяют пару раз. Целенаправлено сразу с опилками присыпать накаленное изделие древесному углем. После чего изделие закаливают восстановительным пламенем горелки. Если в газовую горелку не дать достаточно кислорода, углерод, который есть в ацетилене, не на сто процентов сгорает и может перебегать в состав металла на месте сваривания, т.е. происходит местное неглубокое науглеродование. Когда же сразу применить как присадку металлической провод, который используют в автоматах для наваривания шеек коленчатых и других валов, толщину углеродного пласта можно прирастить до 1-2 мм. Смотрите также термообработка стали.
ometals.ru
Особенности цементирования стали
Необходимо подчеркнуть, что технологический процесс цементации стали — это одна из важных операций нынешней металлургии.? Цементация, как метод термической обработки, имеет ряд собственных конкретных особенностей:
- При организации процесса цементации нужно придерживаться временных и температурных интервалов. Лучшая плотность атомарного углерода достигается в критериях температурного режима от 850 до 950 °C.
- Особенностью диффузного насыщения является относительно маленькая скорость процесса, поглощение поверхностью металлов атома углерода происходит в режиме 0,1 мм/час (показатель меняется зависимо от температуры и среды термической обработки). Так как малая толщина слоя поверхности 0,8 мм, полезные свойства деталь приобретает после 8 часов цементации.
- Состав легированных (инструментальных) и низкоуглеродистых сталей имеет ограниченную долю углерода 0,2?0,25%. Способность всасывать доп атомы газа позволяет отлично использовать способ цементации при термической обработке этих видов стали. Применима обработка машиностроительных, строй и арматурных видов стали марок 20х, 40х. Углеродистые стали способом цементации не обрабатываются.
- Закалка способом цементации осуществляется в присутствии твердого и газового карбюризатора (вещества, способного отдавать атомы углерода). Также насыщение поверхности происходит в кипящей среде, пасте, смесях, содержащих электролит.
Разработка цементации стали. Закалка в домашних критериях видео.
Принципиальным методом улучшения эксплуатационных параметров стали является химико-термическая обработка (ХТО), которая подразумевает воздействие на заготовку реагента при завышенной температуре. В прохладном состоянии сталь характеризуется низкой хим активностью, даже образование ржавчины протекает достаточно медлительно. Чтоб прирастить быстроту реакции, сталь нагревают до высочайшей температуры. Согласно правилу Вант-Гоффа, увеличение температуры на 10° приводит к повышению скорости хим реакции в два раза. Высочайшие температуры позволяют выполнить обработку стали за допустимое время для промышленного производства.
Выбор метода обработки ведется зависимо от хим состава стали
В процессе обработки заготовка находится в среде химически активного вещества. Оно сформировывает на поверхности заготовки слой с особенными качествами, отличающимися от основной части. Почти всегда ХТО позволяет сделать лучше механические характеристики материала, его крепкость, твердость и стойкость к износу.
Самыми пользующимися популярностью процессами ХТО выступают цементация, предполагающая насыщение углеродом, и азотирование, в каком ведется обработка азотом. Также высочайшей продуктивностью обладает нитроцементация, которая совмещает азотирование и цементацию. Обработка другими элементами встречается изредка. Выбор метода обработки ведется зависимо от хим состава стали, от содержания углерода и легирующих веществ.
ХТО является одной из заключительных операций в технологическом цикле производства железных деталей. Она производится после формоизменяющих операций, обработки давлением и резанием. В итоге ХТО деталь приобретает увеличенную крепкость поверхностного слоя, и обработать такую деталь становится еще труднее. ХТО производится таким образом, чтоб коробление поверхности было наименьшим и не требовалось сглаживать поверхность, срезая верхний слой. После ХТО делается только шлифовка поверхности.
Цементация железных изделий
Стали, подвергаемые цементации, можно поделить на три группы по хим составу:
Конструкционные стали, нелегированные либо низколегированные: 15, 18, 20, 20Х, 20ХФ, 20ХМ, 18ХГ, 20ХН. Эти стали имеют низкую цена, но их нереально закалить обыденным методом из-за недостающего содержания углерода, потому насыщение поверхности – обычный метод роста их прочности.
Стали, легированные титаном 18ХГТ, 25ХГТ, 30ХГТ, 20ХНТ, 20ХГНТР. В них появляется особо крепкое соединение – карбид титана.
Высоколегированные конструкционные стали: 12Х2Н4А, 20Х2Н4А, 18Х2Н4ВА, 18Х2Н4МА. Из них изготавливают более крепкие и ответственные детали.
Разработка технологии цементации находится в зависимости от группы, к которой относится сталь. Чтоб получить высшую твердость поверхности, от 58 HRC и выше, обработанную деталь подвергают закалке с следующим низким отпуском. Таким образом, сердцевина детали остается «мягкой» и вязкой, с твердость 35-40 HRC при высочайшей твердости поверхности. Благодаря этому обработанная деталь может употребляться при изгибающих нагрузках, которые небезопасны для хрупких изделий.
Методы выполнения цементации
Большей известностью пользуется газовая цементация. Она производится в печах шахтного типа, другими словами установках, где обрабатываемые детали размещаются ниже уровня пола. Такая конструкция связана с несколькими особенностями процесса. Во-1-х, так проще обеспечить печи плотность. 2-ая причина – газы, воздействующие на металл, имеют огромную плотность, чем у воздуха. Газовая цементация употребляется на заводах, массово производящие упрочненные детали.
Температура при газовой цементации составляет 920-950 °С. Продолжительность обработки находится в зависимости от требуемой глубины цементированного слоя. Средняя скорость диффузионного распространения углерода 0,15 – 0,18 мм/ч. Обычно требуется упрочненный слой шириной 0,8 – 1,5 мм, другими словами длительность процесса может достигать 10 часов. Содержание углерода после обработки в поверхностном слое доходит до 1-го процента. Процесс цементации и следующее термообработка могут производиться 3-мя разными режимами зависимо от степени ответственности деталей. Неответственные детали обрабатывают за 2 нагрева, детали с завышенными требованиями – за 3, а с в особенности высочайшими требованиями – за 4, применяя двойную закалку.
В мелкосерийном производстве достаточно популярен метод цементации с помощью твердого активного вещества, в состав которого заходит древесный уголь и кокс, также катализаторы процесса. Для обработки деталь помещается в железную емкость. Несколько деталей располагаются таким образом, чтоб не касались друг дружку либо емкости.
Температура данного метода несколько выше, чем при газовой цементации. Недочетом процесса является сложность контроля над насыщением поверхности углеродом, что может привести к неравномерной твердости.
samara-metall.ru
Цементация в смесях электролитов [ править | править код ]
Внедрение анодного эффекта для диффузионного насыщения обрабатываемой поверхности углеродом в многокомпонентных смесях электролитов — один из видов высокоскоростной электрохимико-термической обработки (анодный электролитный нагрев
) компактных изделий. Анод-деталь при наложении неизменного напряжения в спектре от 150 до 300 В разогревается до температур 450—1050°С. Достижение таких температур обеспечивает сплошная и устойчивая парогазовая оболочка, отделяющая анод от электролита. Для обеспечения цементации в электролит, не считая электропроводящего элемента, вводят углеродсодержащие вещества-доноры (глицерин, ацетон, этиленгликоль, сахароза и другие).
Читать также: Самодельная коробка для мотоблока
Закалка ножика в графите
В одном из прошедших материалов мы представили обзор видеоклипа по изготовлению ножика из пилы. Таковой ножик имеет толщину клинка 3 мм и если прогреть его до подходящей температуры и резко остудить для закалки, то вероятнее всего клинок вывернет в пропеллер, либо ножик просто лопнет. Потому предлагаем обзор видео по закалке такового ножика в графите. По словам создателя идеи, закалка в графите имеет преимущество в том, что нагрев требуется лишь на режущей кромке клинка. А начнем закалку с просмотра авторского видеоклипа
Нам пригодится:- источник неизменного тока;- незначительно соли;- вода;- графит в пылеобразном состоянии;- маленькой кусочек тряпки;- железный профиль.
Графит можно получить из щеток, применяемых в строй инструментах, также из пальчиковых батареек. Отметим также, что тряпку лучше использовать не синтетическую. Что касается железного профиля, то он будет употребляться для производства корпуса, и его при желании можно поменять уголком.Берем профиль и подсоединяем его к плюсовому контакту источника неизменного тока.Потом берем незначительно соли и растворяем ее в воде.После растворения соли в воде, смачиваем ей тряпку. Это необходимо для того, чтоб сделать типичный предохранитель меж металлами, чтоб обойти ненамеренного прикосновения ножиком о железную заготовку, так как в таком случае возникнет ровная дуга, в итоге чего металл ножика испортится.Отжимаем тряпку и кладем в железный профиль.Засыпаем на тряпку графит.Подсоединяем клинок к минусовому проводу, после этого можно начинать закалку. Становитесь создателем веб-сайта, публикуйте личные статьи, описания самоделок с оплатой за текст. Подробнее тут.
usamodelkina.ru
Методы химикотермической обработки
Производственные циклы металлургической индустрии, обычно, включают цементацию при помощи газовых и твёрдых карбюризаторов.
При первом методе изделие обработки упаковывают в контейнер, заполненный веществом науглероживания (карбюризатором). 2-ой случай предугадывает помещение детали в герметичную печную камеру, за ранее создав в ней определенную атмосферу.
Процесс в жесткой среде карбюризатора
Цементация с внедрением жесткой среды карбюризатора — при таком подходе используют элементы органики (кости, древесную породу и т.д.) и неорганики (кокса) в комплексе с различными активирующими субстанциями. Насыщение углеродом будет происходить сразу с реакцией окисления изотопа. Применение активаторов катализирует процесс поглощения атома углерода железной поверхностью. Способ целесообразен для получения большой глубины проникания частиц в металл. Он оправдывает себя при уникальном изготовлении железных изделий, так как является достаточно трудозатратным и просит издержек времени и энергии.
Читать также: Как подключить 2 двухклавишных проходных выключателей
Газообразная среда термической обработки
Процесс насыщения углеродом, происходящий под воздействием обогащенного природного либо инертного (азот) газа, обширно применяется в масштабном производственном цикле. Выбор газообразной среды находится в зависимости от личных особенностей термической обработки. При всем этом цементируемые стали на базе газов имеют маленькой процент алифатических предельных атомов углеводорода, пропана либо алканов. Этот подход к обработке метала несет немалые валютные издержки и рентабелен только при массовости обработки.
Аналогичный метод используют при тепловом производстве, в раскаленную роторную печь вводят органические высокомолекулярные консистенции скипидара, этилового спирта и т.д., которые распадаются и под воздействием никелевых катализаторов содействуют образованию свободных атомов углерода.
Жидкостная цементация
Для воплощения хим реакции водянистой цементации используют цианидные и бесцианидные ванны. Цианидные ванны систематизируют, как опасные носители не только лишь для экологии, да и для человека. Потому при работе в таких критериях нужно кропотливо придерживаться предписанных мер безопасности во избежание ненужных последствий.
Способ с внедрением бесцианидной ванны наносит загрязнения среды, имеющие необратимые последствия. Методы с внедрением водянистых карбюризаторов если и используют, то в случае получения маленький глубины науглероживания поверхности.
Химико-термическая обработка стали
Благодаря таковой обработке изменяется не только лишь структура металла, да и хим состав его верхнего слоя и деталь может иметь вязкую сердцевину, выдерживающую ударные нагрузки, высшую твердость и износность. Из имеющихся методов химико-термической обработки стали в критериях маленький мастерской можно делать только цементацию. Цементация — это науглероживание поверхности стали. Этому процессу подвергают в большинстве случаев изделия из малоуглеродистых сталей, содержащих менее 0,2% углерода и некоторых легированных сталей. Детали, созданные для цементации, поначалу очищают. Поверхности не подлежащие науглероживанию, покрывают особыми предохранительными противоцементными обмазками.
1-ый состав простейшей обмазки: огнеупорная глина с добавлением 10% асбестового порошка, вода. Смесь разводят до смеси густой сметаны и наносят на нужные участки поверхности изделия. После высыхания обмазки можно создавать последующую цементацию изделия.
2-ой состав используемой обмазки: каолин — 25%, тальк — 50%: вода — 25%. Разводят эту смесь водянистым стеклом либо силикатным клеем.
Цементацию делают после полного высыхания обмазки.
Вещества, которые входят в состав обмазки, именуют карбюризаторами. Они бывают твердые, водянистые и газообразные.
В критериях домашней маленькой мастерской комфортнее производить цементацию при помощи пасты. Это цементация в жестком карбюризаторе. В состав пасты входят: сажа — 55%, кальцинированная сода — 30%, щавелевокислый натрий — 15%, вода для образования сметанообразной массы. Пасту наносят на нужные участки изделия, дают высохнуть. Потом изделие помещают в печь, выдерживая при температуре 900-920°С в течение 2-2,5 часов. При использовании таковой пасты цементация обеспечивает толщину науглероженного слоя 0,7-0,8 мм.
Жидкостная цементация также вероятна в маленькой мастерской при наличии печи-ванной, в какой и происходит науглероживание инструментов и других изделий. В состав жидкости входят: сода — 75-85%, 10-15% хлористого натрия, 6-10% карбида кремния. Печь-ванну заполняют этим составом и погружают изделие либо инструмент. Процесс протекает при температуре 850-860°С в течение 1,5-2 часов; толщина науглероженного слоя добивается при всем этом 0,3-0,4 мм.
Газовую цементацию создают в консистенции раскаленных газов, содержащих метан, окись углерода в особых камерах при температуре 900-950°С и исключительно в производственных критериях. После цементации детали охлаждают совместно с печью, потом закаляют при 760-780°С е окончательным остыванием в масле.
Нагрев заготовки — ответственная операция. От корректности ее проведения зависят качество изделия, производительность труда. Следует знать, что в процессе нагрева металл меняет свою структуру, характеристики и характеристику поверхностного слоя и в итоге от взаимодействия металла с воздухом атмосферы, и на поверхности появляется окалина, толщина слоя окалины находится в зависимости от температуры и длительности нагрева, хим состава металла. Стали окисляются более активно при нагреве больше 900°С, при нагреве в 1000°С окисляемость возрастает в 2 раза, а при 1200°С — в 5 раз. Хромоникелевые стали именуют жаростойкими поэтому, что они фактически не окисляются. Легированные стали образуют плотный, но не толстый слой окалины, который защищает металл от предстоящего окисления и не растрескивается при ковке. Углеродистые стали при нагреве теряют углерод с поверхностного слоя в 2-4 мм.
Это угрожает металлу уменьшением прочности, твердости стали и усугубляется закаливание. В особенности негативно обезуглероживание для поковок маленьких размеров с следующей закалкой.
Заготовки из углеродистой стали с сечением до 100 мм можно стремительно нагревать и поэтому их кладут прохладными, без подготовительного прогрева, в печь, где температура 1300°С. Во избежание возникновений трещинок высоколегированные и высокоуглеродистые стали нужно нагревать медлительно.
При перегреве металл приобретает крупнозернистую структуру и его пластичность понижается. Потому нужно обращаться к диаграмме «железо-углерод», где определены температуры для начала и конца ковки. Но перегрев заготовки можно по мере надобности поправить способом термообработки, но на это требуется дополнительное время и энергия. Нагрев металла до еще большей температуры приводит к пережогу, от чего происходит нарушение связей меж зернами и таковой металл вполне разрушается при ковке. Пережог — непоправимый брак. Если заготовку ковать нагрев до температуры ниже Тн, то это приведет к образованию трещинок.
При температуре на 20-30°С выше температуры Тк в металле происходит раскристаллизация и структура остается тонкодисперсной. На этом шаге нужно заканчивать ковку.
При ковке изделий из низкоуглеродистых сталей требуется меньше число нагревов, чем при ковке подобного изделия из высокоуглеродистой либо легированной стали.
Итак. При нагреве металла требуется смотреть за температурой нагрева, временем нагрева и температурой конца нагрева. При увеличении времени нагрева — слой окалины вырастает, а при насыщенном, резвом нагреве могут показаться трещинкы. Понятно из опыта, что на древесном угле заготовка 10-20 мм в поперечнике греется до ковочной температуры за 3-4 минутки, а заготовки поперечником 40-50 мм прогревают 15-25 минут, отслеживая цвет каления.
www.kefa.ru
Карбонитрация стали
Пользующимся популярностью видом ХТО стали и чугуна фактически всех марок является карбонитрация, либо жидкостное азотирование. В данном случае поверхностный слой заготовок насыщается углеродом и азотом в соляных расплавах при температуре 560-580°C. Соляные составы синтезированы из аммоноуглеродных соединений: меламина, мелона, дициандиамида. Карбонитрация сходна с цианированием. Но цианирование осуществляется с внедрением ядовитого цианида натрия при температурах до 860°C. Для карбонитрации используют неядовитые соединения, осуществляется она при температурах до 570°.
Читать также: Как правильно собрать болгарку
Достоинства технологии карбонитрации стали
- Одновременное насыщение азотом и углеродом инициирует возникновение карбонитридных фаз – более пластичных и наименее хрупких, по сопоставлению с чисто нитридными.
- Карбонитрация – более экономный процесс, благодаря его маленькой продолжительности – 0,5-4 часа.
- Равномерность нагрева и диффузии.
- Отсутствие тепловых напряжений, обеспечивающее малые деформации и точность геометрических характеристик в границах микронов.
- Улучшение усталостной прочности изделий до 80%, износостойкости, коррозионной стойкости.
- Уменьшение коэффициента трения до 5 раз.
- Отсутствие хрупкости поверхностного слоя, насыщенного карбонитридами.
- Возможность обработки дешевых низкоуглеродистых сталей, которые не упрочняются обычным азотированием. В итоге карбонитрации они получают свойства, которыми владеют более дорогие и ужаснее обрабатываемые стали.
- Этот процесс для рядовых деталей является финальным, не требующим доп механической обработки. Ответственные изделия после карбонитрации подвергают хонингованию – полировке на 1-2 мкм.
Комбинированное насыщение поверхности азотом и углеродом может применяться даже для высоколегированных и устойчивых к коррозии сталей. На их поверхности находится уплотненная пленка из окислов хрома и других легирующих добавок, противодействующая процессу незапятнанного азотирования.
Этапы карбонитрации
Доп плюсом этой технологии является возможность частичного погружения детали в солевой расплав, что позволяет упрочнить только отдельные участки.
- На карбонитрацию поступают детали с окончательными размерами. По мере надобности оставляют малый припуск на посадочных поверхностях для полировки.
- Подготовительные мероприятия: чистка, обезжиривание.
- Нагрев в печи и карбонитрация.
- Остывание в воде, масле, на воздухе.
- Промывка, сушка.
Таким методом обрабатывают:
- режущий инструмент;
- пресс-формы;
- пары трения;
- элементы зубчатых передач;
- детали насосов.
Принципиальный плюс этой технологии – соответствие экологическим нормам и безопасность работников, благодаря отсутствию ядовитых соединений в насыщающих средах. Карбонитрация применяется как на больших промышленных предприятиях, так и в маленьких мастерских и в домашних критериях.
Закалка и науглероживание металлов — Кустарь
Закалка имеет целью придать стали необыкновенную твердость, характерную стали, нагретой выше 700 °C и стремительно охлажденной. При операциях закалки огромное значение имеет верный накал металла (отсутствие пережога) и равномерное резвое остывание. При накаливании металла следует избегать лишнего окисления поверхности. Идеальнее всего накаливаемую сталь покрывать особенным составом, который содержит внутри себя углерод. Углерод этот перебегает в сталь (науглероживание) и докладывает ей необыкновенную твердость. 1. Ванны для закаливания по Шену. Примененная опытнейшей рукою водяная баня является самым дешевеньким средством для закаливания металлов. Необходимо только позаботиться, чтоб водяная баня была длительное время схожей температуры, идеальнее всего 27°. При более теплой воде металл делается ломким, при жаркой воде — недостаточно жестким. Прибыльнее всего при каждом сорте продукта пробным опытом установить верную температуру и уже держаться ее при работе. 2. Особенный прием закалки стали. Как понятно, стали можно придать методом особенной закалки такую твердость, что она будет резать стекло, подобно алмазу. Но не многим понятно, что для сообщения стали таковой твердости существует обычной метод. Шило, лезвие ножика либо другой инструмент следует накалить до ярко красноватого свечения и тотчас же опустить в обычный сургуч на одну только секунду. Операцию погружения в сургуч необходимо повторить пару раз, выбирая всякий раз для погружения свежее место в сургуче до того времени, пока сталь не остынет и не будет уже более заходить в сургуч. Тогда процесс закалки считается законченным. Остается очистить приставшие частички сургуча. При употреблении закаленного таким методом острия либо лезвия из стали, советуется всякий раз смачивать его скипидаром. 3. Составы для науглероживаиия закаливаемой стали. а) Неплохим составом для науглероживания закаливаемой стали быть может последующий: берут 1 толченого стекла, 200 поваренной соли, 8 животного угля, 2 древесного угля, 2,5 ржаной муки, 25 канифоли и 1200 желтоватой кровяной соли, растирают все составные части в порошок и замешивают в спирте до получения густого теста. Этим составом Покрывают железные предметы перед закалкой. В особенности подходящ он для инструментов, как напр., ратфилей и т. п. б) Заместо обозначенного выше рецепта можно применить последующий. Берут 700 канифоли, 300 железисто- синеродистого калия (желтоватой кровяной соли), 100 медного купороса и 100 льняного масла. Эти составные части, начиная с канифоли, варятся в горшке при неизменном помешивании (по Бруккерту) до того времени, пока остается остаток в 1000 (улетучивают таким образом 200). Массу выливают в ящики, где она затвердевает. Чтоб закалить инструмент, его нагревают до вишнево-красного каления и втыкают в массу, которая под воздействием нагретого инструмента становится сразу мягенькой. Неплохую сталь снова нагревают и погружают потом в прохладную воду, отчего сталь становится очень упругой. Сталь худшего свойства необходимо 2 — 3 раза попорядку погружать, всякий раз перед этим накаливая ее, в закаливающуюмассу. 4. Закалка ратфилей. Ратфили обсыпаются консистенцией из 5 роговой муки, 5 древесного угля в порошке, 2 поваренной соли в порошке и 1 железисто-синеродистого Калия (желтоватой кровяной соли). Создатель: Г. Бродерсен |
www.sdelaysam.info
Газовая цементация
В машиностроении всераспространена разработка насыщения верхнего слоя железных изделий углеродом в атмосфере углеродосодержащих газов. Понятно, что такое создание комфортно для массовой обработки деталей, потому что:
- Допускается регулирование плотности газов; тем формируется углеродистый слой с данными качествами.
- Полный цикл термической обработки (цементация, закалка, промывка и отпуск) проходит в одном месте — в шахтной (цементационной) печи.
- Процесс экономичен, механизирован и автоматизирован.
- Коробы с карбюризатором не нуждаются в прогреве, что уменьшает время протекания цементации.
- Скорость науглероживания деталей увеличивается в 2 – 3 раза (сравнивая с другими способами), однородность слоя выше.
- Температуру газовой консистенции углеводородов (метан и окись углерода), доводят до 900-950°С.
- После цементации технологическую цепочку завершает отпуск (закаливание).
Сталь — Советы мастеру
Термообработка стали. Отжиг — нагревание железного изделия до температуры 700—900°С (зависимо от марки стали) и остывание совместно с печью. Отжиг используют при изготовлении из 1-го закаленного изделия другого либо в случае неудачной закалки.Если закаливать неотожженные изделия, в них могут появиться трещинкы, структура металла станет неоднородной, что резко усугубляет качество изделия.Маленькие детали отжигают, нагревая их на мощных железных плитах, которые за ранее раскаляют. После чего детали медлительно остывают сразу с плитой. Время от времени изделие нагревают ацетиленовой горелкой, которую позже равномерно убирают от изделия, делая процесс его остывания неспешным. Этот способ используют для отжига маленьких стальнУх деталей.Нормализация — нагрев стали до температуры 900°С с следующим остыванием на воздухе (в обычных критериях) для улучшения внутренней микроструктуры стали и увеличения механических параметров, также для подготовки ее к следующей термообработке.Закалка заключается в придании железному изделию высочайшей прочности и твердости. Но при закалке сталь становится более хрупкой. Этот недочет ликвидируют в процессе отпуска стали.При закалке изделие нагревают до высочайшей температуры, а потом стремительно охлаждают в особых охлаждающих средах. Зависимо от режима закалки у изделия из одной и той же стали можно получить разные структуры и характеристики.Для заслуги лучших результатов железное изделие нагревают до температуры 750—850°С. Разогрев должен происходить умеренно. Потом нагретое изделие стремительно охлаждают до температуры около 400°С. Скорость остывания должна быть не меньше 150°С за секунду, другими словами остывание изделия должно произойти в течение всего 2—3 с. Предстоящее остывание до обычной температуры может протекать при хоть какой скорости, потому что приобретенная при закалке структура достаточно устойчива и скорость предстоящего остывания на нее не оказывает воздействия.В качестве охлаждающих средств в большинстве случаев употребляют воду и трансформаторное масло. Скорость остывания в воде больше, чем в масле: при температуре воды 18°С скорость остывания добивается 600°С за секунду, а в масле — 150°С. Время от времени для увеличения закаливающей возможности в воду добавляют поваренную соль (до 10 %) либо серную кислоту (10—12 %), к примеру, при закалке плашек и метчиков. Более высочайший нагрев, чем это нужно, равно как и чрезмерная скорость остывания в прохладной воде, приводит к ненужным результатам — деформации стали и возникновению в ней паразитных напряжений.При закалке инструментов из углеродистой стали используют закалочные печи с температурой нагрева до 900°С, а для нагрева легированных и быстрорежущих сталей — до 1325°С. Печи для закалки бывают последующих видов: камерные, либо огненные, в каких изделия нагревают открытым пламенем; муфельные, нагревающие за счет сопротивления электронных обмоток; печи-ванны, представляющие из себя тигли, заполненные расплавами солей, к примеру хлористым барием.Закалочное нагревание в ваннах комфортно вследствие того, что температура содержащегося в ней расплава всегда постоянна и закаливаемое изделие не может нагреться выше этой температуры. Не считая того, нагрев в водянистой среде происходит резвее, чем в воздушной. В маленьких мастерских целенаправлено использовать для закалочного нагрева муфельные электронные печи, к примеру МП-8. Инструмент либо деталь помещают в прохладную муфельную печь, позже ее включают и начинают медлительно нагревать до требуемой температуры. Так как время нагрева длительно, внутренние напряжения, возникающие в изделии, малы.После закалки изделия создают его отпуск. Он смягчает нехорошие явления при закалке, увеличивает вязкость и уменьшает хрупкость изделия. Не считая того, отпуск избавляет огромную часть внутренних напряжений, появившихся при закалке.Для определения температуры при отпуске изделия пользуются цветами побежалости. Если очищенное от окалины железное изделие подогреть до 220°С, на нем появляется узкая пленка оксидов железа, придающая изделию разные цвета — от желтого до сероватого. С увеличением температуры либо повышением времени пребывания изделия при данной температуре окисная пленка утолщается и цвет ее меняется. Цвета побежалости идиентично появляются как на сырой, так и на закаленной стали. При отпуске закаленных изделий используют два метода:1. Поверхность закаленного изделия отлично отшлифовывают маленькой шкуркой и нагревают. По мере того как температура нагрева увеличивается, на незапятанной поверхности изделия возникают цвета побежалости. Когда изделие будет нагрето до определенной температуры и появится подходящий цвет, его стремительно охлаждают в воде2. При закалке многих инструментов, к примеру чеканов, штихелей, резцов, молотков и т. п., требуется, чтоб закаленной была только рабочая часть, а сам инструмент оставался бы незакаленным, сырым. В данном случае закалку создают так: инструмент нагревают незначительно выше режущего (рабочего) конца до требуемой температуры, после этого опускают в воду только рабочую часть, а металл выше рабочей части остается жарким. Вынув инструмент из воды, стремительно зачищают его рабочую часть (наждачной шкуркой либо трением о землю). Тепло, оставшееся в неохлажденной части, подымет температуру охлажденного конца, и после возникновения на нем подходящего цвета побежалости инструмент совсем охлаждают.Образование на поверхности изделия окалины приводит к угару металла, деформации, уменьшению теплопроводимости, что понижает скорость нагрева изделия в печи. Не считая того, растет твердость и затрудняется механическая обработка. Окалину убирают с изделий либо механическим методом, либо травлением.Обезуглероживание стали заключается в выгорании углерода с поверхности изделия. Обезуглероженный слой обладает пониженными прочностными чертами. Интенсивность, с которой происходит окисление и обезуглероживание, находится в зависимости от состава атмосферы печи и температуры нагрева. Чем выше нагрев, тем процессы идут резвее Чтоб обойти образования окалины при нагреве, под закалку время от времени используют пасту, состоящую из водянистого стекла — 100 г, огнеупорной глины — 75 г, графита — 25 г, буры — 14 г, карборунда — 30 г, воды — 200 г.Пасту наносят на изделие и дают ей просохнуть, потом изделие нагревают обыденным методом. После закалки его промывают в жарком содовом растворе. Для предупреждения образования окалины на инструментах из быстрорежущей стали нередко используют покрытие бурой. Для этого инструмент, подогретый до 850°С, погружают в насыщенный аква раствор либо порошок буры.Сейчас разглядим особенности закаливания некоторых железных изделий. Углеродистые стали при закалке лучше охлаждать поначалу в воде до температуры 400—350°С, а позже в масле. Это предутверждает появление внутренних напряжений. Во время остывания изделие рекомендуется стремительно передвигать сверху вниз.Тонкостенные длинноватые детали (к примеру, ножики) при охлаждении опускают в воду либо масло строго вертикально, в неприятном случае они могут очень деформироваться.Зубила целенаправлено закаливать в влажном песке, который увлажняют веществом соли.Тонкие сверла закаливают в сургуче. Для этого нагретый до красного цвета конец сверла погружают в сургуч и оставляют там до полного остывания.
sovmasteru.ru
Применение газа
В массовом производстве употребляется газовая среда. Проводить насыщение поверхности углеродом можно только при использовании герметичной печи. Более всераспространенным составом газовой среды можно именовать вещества, получаемые при разложении нефтепродуктов.
Газовая цементация стали
Процедура имеет последующие особенности:
- Следует использовать конвейерные печи непрерывного деяния с завышенной изоляция рабочей среды. Они очень изредка инсталлируются в домашних критериях из-за высочайшей цены.
- В печь помещают заготовки, после этого проводится нагрев среды до требуемой температуры.
- После нагрева печи до требуемой температуры подается газ.
Преимуществ у схожей технологии достаточно много:
- Нет необходимости в долговременной подготовке газовой среды.
- Процесс предугадывает малую выдержку, что понижает издержки на поддержание температуры.
- Оборудование малогабаритное, не занимает много места.
Но есть значимый недочет, который заключается в отсутствии способности установки оборудования и налаживания процесса в домашних критериях. Рентабельность цементации в домашних критериях при установке подобного оборудования обеспечивается только при существенном увеличении обрабатываемых партий.
Если вы отыскали ошибку, пожалуйста, выделите кусок текста и нажмите Ctrl+Enter.
Существует огромное количество подходов к обработке конструкций из металла. Одним из них является цементация стали — химикотермический процесс насыщения металла свободным углеродом для улучшения его физических параметров, прочности поверхности и пластичности сердцевины.
Детали и механизмы, работающие в критериях завышенного трения и вибрации, испытывающие механические удары, сначала подлежат схожей термической обработке. Перед проведением работы следует знать, какие стали подвергаются цементации и в чем заключается главная специфичность этой технологии обработки металлов.
Науглероживатель: создание, особенности, применение
В процессе выплавки чугунов и сталей углерод вводят в расплав либо подают на зеркало металла в момент его разлива. Для этого используют особые углеродсодержащие материалы, которые именуют науглероживателями (либо карбюризаторами). Науглероживатель присваивает сплавам железа доп крепкость, твёрдость, понижает их вязкость и пластичность, также предупреждает окисление отливок во время остывания.
В качестве карбюризаторов интенсивно применяется искусственный размельченный графит различных марок.
В жестком карбюризаторе (жесткая)
В качестве среды-донора углерода используют древесный уголь; как вариант — торфяной кокс, каменноугольный полукокс. Смесь дополняют активизаторами (углекислый натрий, барий либо кальций).
Для высококачественного насыщения уголь размельчают до частиц размером 3-10 мм, а потом просеивают, чтоб избавиться от пыли. Активизаторы также размельчают и просеивают, стремясь придать солям вид маленького порошка.
Процесс цементации стали проходит в несколько шагов:
- Предметы, очищенные от эмульсии и масла, загружают в ящик из стали, с карбюризатором, который должен на сто процентов их покрывать. Нельзя допустить их касания стен ящика и друг дружку.
- Емкость помещается в печь. Ее плотность обеспечивается притертой крышкой, глиной либо песочным затвором.
- Начав с подготовительного прогрева, температуру увеличивают до технологических 900-950°C.
- Вероятен ускоренный вариант (при 980°C), сокращающий время насыщения в 2 раза, но вызывающий образование карбидной сетки (возникающей из-за очень высочайшего углеродного насыщения). Для ее устранения и исправления структуры проводят доп многоэтапную обработку (нормализацию).
Цементация стали в домашних критериях организовывается в жесткой среде либо с внедрением графита. Оба варианта доступны и не требуют особых знаний. Облагораживание помещения для первого метода очень упрощается, так как печь не нуждается в обеспечении высочайшей плотности.
Это условие полностью достижимо в домашней мастерской. Невзирая на тривиальные достоинства, у способа есть и недочеты: трудозатратность и низкая производительность.
Перед обжигом готовится жесткая смесь (карбюризатор). Она состоит из консистенции древесного угля с углекислыми солями бария, натрия либо кальция. Соли за ранее размельчают до пылеобразного состояния, а потом просеивают, чтоб достигнуть однородности. Толика древесного угля в консистенции — 70-90%, остальное приходится на соли.
Смесь создается одним из 2-ух методов:
- Соль и древесный уголь кропотливо перемешиваются. Если смесь будет недостаточно однородной, во время цементации различные участки поверхности детали будут всасывать различное количество газа. В итоге на изделии образуются пятна, сигнализирующие о недостаточной концентрации углерода; качество поверхности будет неравномерным.
- Уголь пропитывают солью, растворенной в воде. Потом его подсушивают до получения консистенции, влажность которой не превосходит 7%. Таковой состав выходит однороднее и лучше подходит для использования дома.
Этапы цементации в жесткой среде:
- Изделие очищается от загрязнений и укладывается в железный короб, засыпается жестким карбюризатором (порошковой консистенцией). Нужно смотреть, чтоб меж стенами и ним сохранялся просвет в 2-2,5 см. Размер ящика должен соответствовать форме предмета; это уменьшит время прогрева и сделает лучше качество цементированного слоя.
- Короб накрывается подогнанной крышкой, ее края промазываются глиной для плотности (от утечки газов).
- Емкость помещают в за ранее прогретую печь. Цементация запускается при температуре 850-920°C.
- Атомы углерода поглощаются раскаленным верхним слоем.
Жесткая цементация стали допускает многократное внедрение карбюризатора. Для повторного отжига к отработанному карбюризатору достаточно добавить до 30% свежайшей консистенции.
Для большинства ответственных машинных деталей (валы, поршневые пальцы, зубчатые колеса, лемехи, шпиндели) достаточной считается глубина цементированного слоя от 0,6 до 2 мм. Время выдержки для приобретения достаточной твердости может варьироваться от 6 до 20 часов.
Изделия после цементации в жестком карбюризаторе получаются крепкими, но хрупкими. Чтоб избавится от ненужного характеристики, детали подвергают термической обработке (закалке) с нагревом до 840-850°С, с следующим отпуском (нагревом до 780-800°С), снимающим внутренние напряжения.
Источник: vsamodelino.ru
Возможно интересно:
Смотрите также:
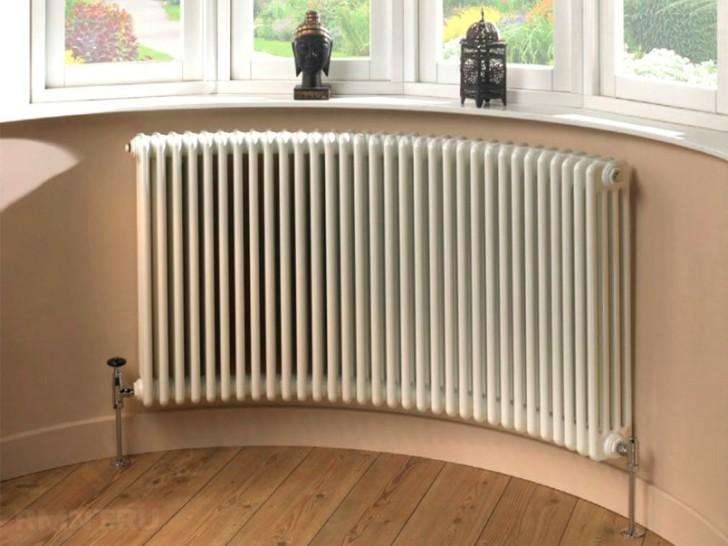
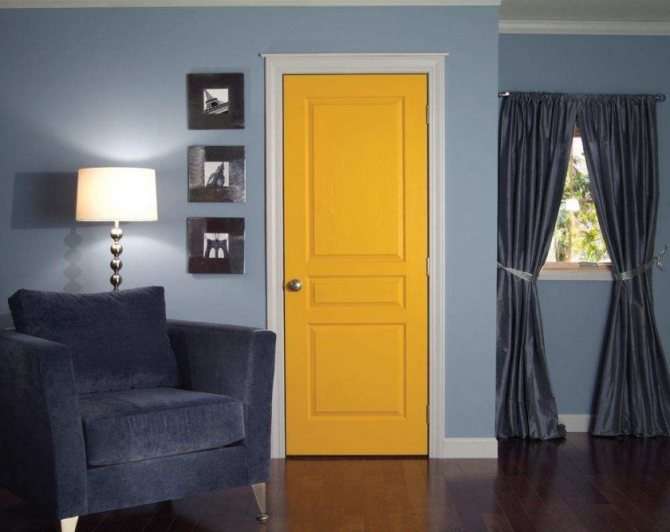
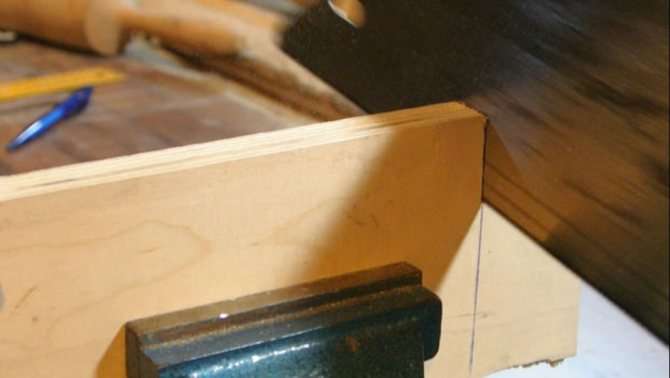
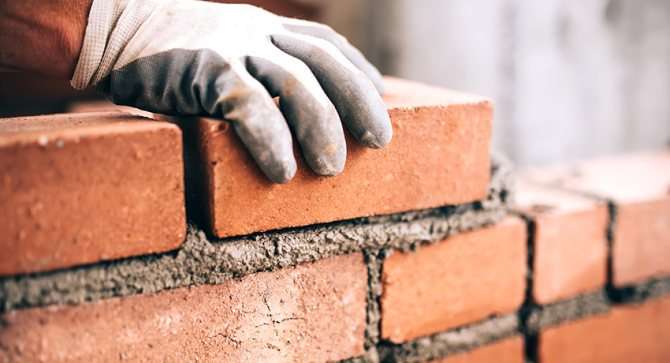
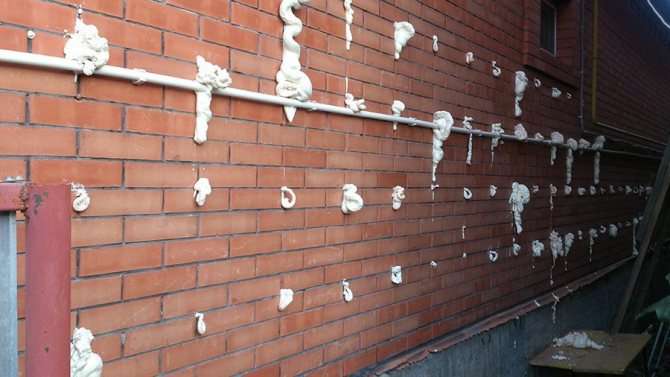
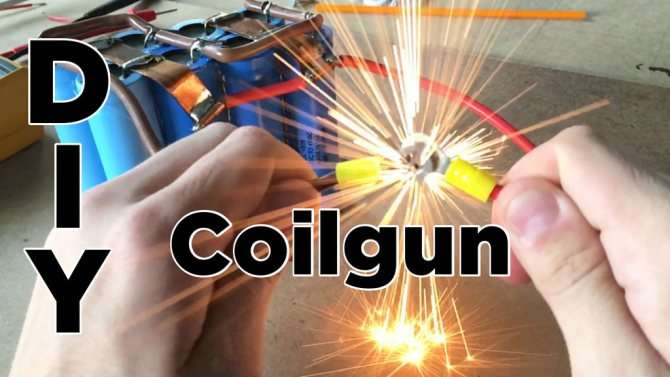